Aluminum Hard Coat Anodized
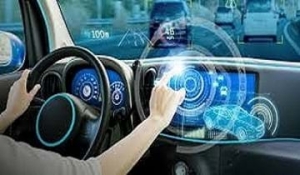
Aluminum Hard Coat Anodized
Product Features Width [mm] 38 Height [mm] 6 Length [mm] 131 Material Aluminum 6061-T6 Surface MIL-A-8625 Type III Class 1 Weight [g] 83 Description: MIL-A-8625 Type III Class 1 (Non-Dyed) and Class 2 (Dyed) Magntek Electronic Inc. offers aluminum hard coat anodizing (Type III) at our state-of-the-art facility in Taiwan. We also provide standard aluminum anodizing (Type II) services. Hard Coat Aluminum Anodizing Aluminum Hard Coat Anodizing is similar to standard anodizing in that both are controlled electrochemical processes. The key difference is that hard coat anodizing provides a surface that is more wear resistant and has a smoother and harder surface than standard anodizing. Modified hard coat anodizing which sometimes called hard coating or hard anodizing is an electrochemical process that provides corrosion protection to aluminum and aluminum alloy parts or pieces During the hard coat anodizing process, a uniform aluminum the oxide layer is formed on the surface that penetrates into the material. The hard coat anodizing process involves submerging the part(s) in a sulfuric acid bath at approximately 32°F, with a density of 23 to 37 amps, for anywhere from 22 minutes to two hours. The amount of time spent submerged determines the thickness of the coating. While aluminum naturally forms the oxide on the surface over time, the aluminum oxide that is formed on the surface during the hard coat anodizing process is more uniform, dense, and much harder than with natural oxidation. Hard Coat Anodized Aluminum is used for the following reasons: Corrosion resistance Increase wear resistance Increase hardness Electrical Resistance Lightweight properties Flame resistance Temperature Resistance ISO 9001 2015 certificated
Send Enquiry