Hot Coil Spring
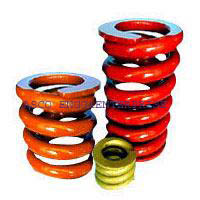
Hot Coil Spring
Spring Design and Specifications:- In Ordering Give the Following Information as Completely as Possible:Free Length, Maximum, Minimum. Controlling Diameter, Outside Diameter Maximum. Inside Diameter Minimum. Pitch Diameter. Works Inside (Dia. Hole). Works Over (Dia. Shaft). In these products, the gap between the successive coils is larger These products are manufactured using round wire and wrapped in cylindrical shape with a constant pitch between the coils On applying the load, the spring contracts in action Capacity: Bar dia. 1 mm upto 62 mm Out side dia. 20 mm upto 500 mm. Free height 10 mm upto 1500 mm Total coils as applicable Load bearing capacity upto 40tons. per pc Material Section: Round, Square, Rectangular taper, Flat or any special shape Grade: 1mm upto 12mm IS:4454Pat-1 & Part-IV and 12mm upto 62mm Silico-Manganese steel 970/55 En-45, IS:3195 Gr.55Si7 and Gr.60Si7 Chrome - Vanadium Steel BS:970/55 En-47, IS:3195 Gr.50Cr4V2 and Gr.60Cr4V2, IS:5160, Sup-9 and SAE-4161H Status of finish: shot peened, if required Shot peening operation is followed as per IS:7001 to improve the fatigue Solid Height The solid height of a compression spring is defined as the length of the spring when under sufficient load to bring all coils into contact with the adjacent coils and additional load causes not further deflection. Solid height should be specified by the user as a maximum, with the actual number of coils in the spring to be determined by the spring manufacturer. As square or rectangular wire is coiled, the wire cross-section deforms slightly into a keystone or trapezoidal shape, which increased the solid height considerably. The dimensional change is a function of the spring index and the thickness of the material. Compression Spring Ends There are four basic types of compression spring ends as shown above. The particular type of ends specified affect the pitch, solid height, number of active and total coils, free length and seating characteristics of the spring. End Coil Effects A compression spring cannot be closed and ground so consistently that its ends will always be square (in parallel planes at right angles to its axis). In addition, the helix angles adjacent to the end coils will not have uniform configuration and closing tension, and these springs cannot be coiled so accurately as to permit all coils to close out simultaneously under load. As a result of these end coil effects, the spring rate tends to lag over the initial 20 percent of the deflection range, often being considerably less than calculated. As the ends seat during the first stage of deflection, the spring rate rises to the calculated value. In contract, the spring rate for the final 20 percent of the deflection range tends to increase as coils progressively close out. The spring rate over the central 60 percent of the deflection range is essentially linear. If possible, critical loads and rates should be specified within this range, which can be increased to about 80 percent of total deflection by special production techniques. However, these techniques add substantially to manufacturing cost and are usually unwarranted. Squareness of Ends, Grinding, and Degree of Bearing The squareness of compression spring ends influences the manner in which the axial force produced by the spring can be transferred to adjacent parts in a mechanism. There are some types of applications where open ends may be entirely suitable. However, when space permits, closed ends afford a greater degree of squareness and reduce the possibility of tangling with little increase in cost. With closed ends, the degree of squareness depends on the relationship of the wire diameter (d) and the mean coil diameter (D). Unground springs with indexed (D/d) that are low have less squareness, while unground, high-index springs have more squareness. Compression springs with closed ends can often perform well without grinding, particularly in wire sizes smaller than .020 in. or spring indexes exceeding 12. Many applications require grinding the ends in order to provide greater control over squareness. Among these are applications in which (1) high-duty springs are specified, (2) unusually close tolerances on load or rate are needed, (3) solid height must be minimized, (4) accurate seating and uniform bearing pressures are required, and (5) a tendency toward buckling must be reduced. Since springs are flexible and external forces tend to tilt the ends, grinding the extreme squareness is difficult. A spring may be specified for grinding square in the unlaoded condition or square under load, but not in both conditions with any degree of accuracy. When squareness at a specific load or height is required, it should be specified. Well-proportioned, high-quality compression springs which are specified with closed and ground ends should have the spring wire at the ends uniformly taper from the full wire diameter to the tip. A slight gap, which occasionally opens during grinding, is permissible between the closed end coil and the adjacent coil. The bearing surface provided by grinding should extend over a minimum of 240 degree of the end coils. Results will vary considerably from these nominal attainable values with springs in smaller wire sizes or with higher indexes. In general, it is impractical to adhere to a general rule regarding "degree of bearing" since process capabilities depend so much on the individual configuration of the spring.
Send Enquiry